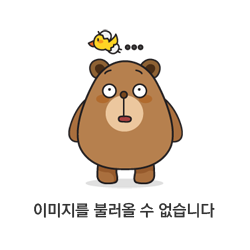
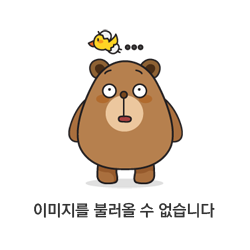
표면다듬질에 대하여 알아보려고 한다. 피삭성은 가공공정 후에 표면다듬질에 의하여 평가되는 경우가 많다. 좋은 표면다듬질은 단인공구나 다인공구 가공에서 많은 변수에 의하여 영향을 받는다.
표면다듬질
표면다듬질을 개선시키는 인자는 경절삭, 작은 이송, 높은 절삭속도, 절삭유제, 끝이 둥근 공구 및 잘 연삭 된 공구의 증가된 윗면경사각이다. 이 특징의 다수는 매우 바람직하지만 공구수명을 단축시키고, 절삭력을 증가시키며 전체적으로 비경제적일 수 있다. 공기에 인접하는 본체의 최외부의 경계를 표면이라고 한다. 이 표면이 날카로운 절삭날에 의하여 변형될 때, 표면다듬질이란 용어는 경계를 말한다. 공구와 접촉하고 있는 회전원통체의 기존 표면이 제거될 때 기저의 표면이 새로운 경계를 형성한다.
이 표면을 여러 배 확대한다면 연속적인 톱니모양의 산맥외양이 나타난다. 산맥모양 단면의 불규칙한 자연적인 외양과 같이 보이지만 수학적인 형식과 지형적 형태를 르 나타낸다. 이 유사성은 선반에서 공구에 의해 선삭 되는 홈의 현미경 조직으로 확장된다.
현재의 기술에 있어서 표면다듬질의 중요성은 고객과 기술자 모두에 의하여 인식된다. 지나친 다듬질은 비용이 과대해질 수 있다. 한편 표면 다듬질은 치수정밀도에 영향을 미친다. 피로, 경도, 열전달 등의 기술적 특성은 표면 다듬질에 의하여 영향을 받는다. 표면거칠기는 전자적 및 시각적으로 측정된다. 비파괴 표면검사 장치는 광속절단원리에 의하여 그림 1에 나타내었다.
이 원리에 따르면 재래식 방법에서 문제로 되었던 접촉이나 긁힘 없이 표면을 통과하여 광학적 절단이 된다. 측정에 있어서 백열등 Q는 슬릿 S를 비춘다. 면도날 같은 빛이 대물렌즈 O₁을 통과하여 공작물 표면에 45° 각으로 투사된다. 이 광속은 45° 반대각에서 현미경을 통하여 관찰된다. 현미경 대물렌즈 O₂는 O₁과 같은 배율을 가진다. 이 얇은 광속은 봉우리와 골을 관찰할 수 있고, 접안렌즈 EP 내의 교차 CL은 시야범위 안에서 옮길 수 있다. 거칠기의 높이, 즉 봉우리에서 골까지의 거리와 거칠기 폭의 두 가지 측정이 가능하다. 이 측정기는 미크론 차원까지 측정할 수 있다. 이 방법으로 공구 선단 형상에 합리적으로 일치하는 표면 다듬질 효과를 찾는 것이 가능해진다.
이상적인 표면은 공구의 기하학적인 인자가 제시하는 바와 같이 정확히 기계가공된다고 가정된다. 채터 또는 구성인선의 효과 또는 공구마멸 효과는 무시된다. 선삭에서는 공구선단은 공작물 표면 위에 나사의 나선을 형성하나 표면에 대한 공구의 침입은 깊이가 얕으므로 나사산이 뚜렷하게 나타나지 않는다. 회전하는 봉재에 대한 단인공구 효과에 대해서는 그림 2에서 확인하라.
기하학적 상사관계를 사용하여 이상적인 표면의 모델을 만들 수 있다. 다듬질 작업에서 보편성이 있는 두 가지 공구의 기하학적 모양을 그림 3에서 나타내었다. 그림 3의 A에 나타낸 공구 모델에 대한 최대 표면거칠기는 다음 식과 같이 주어진다.
H𝓂𝚊𝘹 = f/(tan C𝚜 + cot C𝚎)
여기서,
- f = 이송량(in.)
- C𝚜 = 옆면절삭날각(°)
- C𝚎 = 앞면절삭날각(°)
공구의 표면기하학은 다음과 같다
H𝓂𝚊𝘹 = f²/8r
여기서,
- r = 공구반지름(in.)
H𝓂𝚊𝘹 는 거리가 중심선 거칠기 데이터에 의하여 측정되는 산술평균과 다르다. 그러므로 이 측정치는 H𝓂𝚊𝘹와 비교하기 위하여 2를 곱해야 한다. 예로써 이송이 0.008 in.이고 C𝚜 = C𝚎 = 15°라고 가정하면 최대 거칠기는 0.002in.이며 정밀한 다듬질은 아니다. 한편 노즈가 둥근 공구, 예를 들면 반지름이 1/32in. 이면, 0.000256 in. 의 최대표면높이가 되고, 앞의 공구보다 8배 정도 정밀하게 된다. 단, 이 값들은 이상적인 숫자를 나타내며, 실제로 작업자는 표준방법을 사용하여 정상상태 거칠기를 결정하게 된다. 만약 거칠기가 예정된 공구형상, 이송, 공구와 공작물 재료에 대한 값을 초과하면, 그 작업은 피삭성 표준을 초과한 것이다.
'기계제작법' 카테고리의 다른 글
터릿선반에 대해서 공부하기 (0) | 2024.12.21 |
---|---|
보통선반에 대하여 공부하기 (0) | 2024.12.20 |
공구수명에 대하여 공부하기 (0) | 2024.12.19 |
절삭에 필요한 냉각제와 피삭성에 대하여 공부하기 (0) | 2024.12.19 |
칩의 형태와 생성에 대하여 공부하기 (0) | 2024.12.17 |