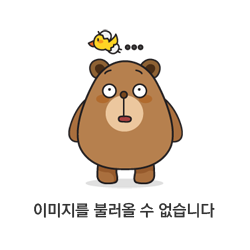
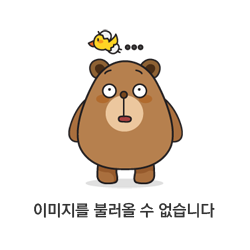
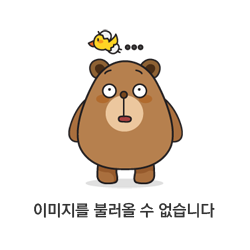
금속절삭 공구에 대하여 알아보고자 한다. 금속절삭 공구의 성공적인 적용은 공구 형상, 공구와 공작물의 재질, 냉각제, 공작기계 및 여러 다른 인자에 의존한다. 효과적인 공구의 특성에는 고온경도, 마멸저항, 인성, 저마찰, 비용이 포함된다.
절삭공구 형상
선반에서 사용되는 것과 같은 단인공구의 절삭작용을 이해하기 위하여 그림 1을 참조한다. 이 그림은 용접된 초경팀 공구를 나타내는데, 단인으로 분류되고, 절삭도중 한 절삭날이 작용한다. 공구는 형상과 재질로 기술되는데, 공작기계와 공작물 재질에 따라 매우 다양한다.
옆면절삭날각은 0~90° 까지 변할 수 있으며 칩의 두께와 폭에 영향을 준다. 칩이 길고 얇을 수록 아래쪽의 압력이 더 긴 길이에 걸쳐 분포하고, 절삭날이 칩의 힘에 의하여 파손되는 것이 덜해지기 때문에 공구수명을 증가시킨다. 난삭재를 가공 할 때 옆면 절삭날 각을 감소시키거나 이송을 증가시키면, 공구수명이 증가될 수 있다. 옆면 절삭날각이 0° 일때, 절삭날의 전체길이가 한꺼번에 공작물과 접촉하고 강한 초기 충격을 받는다. 옆면절삭날각이 30° 이면 공구는 금속으로부터 더 작은 초기 충격을 받는다.
옆면여유각은 공구 파손을 막고 공구 수명을 증가 시킨다. 이 각이 너무 작으면, 공구는 공작물과 마멸을 일으키고 과도한 열을 발생하며 공구가 빨리 무뎌지게 된다. 냉강철에 대한 옆면여유각은 2~4°, 경강에 대하여는 4~6°, 비철재료에 대하여는 7~12° 이다.
앞면여유각은 공구가 공작물과 마찰하지 않고 절삭할 수 있도록 해준다. 윗면경사각이 노즈를 향하여 아래쪽이면 음의 윗경사각이다. 기울기가 노즈에 뒤쪽에 향하면 양이다. 이 각은 칩의 유동을 제어한다. 양의 각도는 칩을 공작물의 가공 평면에서 떨어지게 하고, 음의 윗면경사는 칩을 공작물 쪽으로 움직이게 한다. 5°의 양의 윗면경사는 칩을 치우도록 움직이게 하여 칩이 가공평면을 훼손하는 것을 막는다. 이 각이 음이면, 공구를 튼튼하게 하고, 특히 단속절삭의 경우에 공구 수명을 늘려준다.
삽입팁
단체 단인공구 외에 초경합금 팁을 공구몸체에 경납 땜하거나, 그림 2와 같이 공구고정구에 삽입하여 고정한다. 여러 가지 종류의 공구고정구와 삽입팁이 사용된다. 삽입팀은 마멸되면 버리며 다른 팁으로 교체하고, 공구몸체는 계속사용한다. 일반적으로 삽입식이 경난땜 공구보다 더 경제적이다. 삽입식은 여러 개의 날이 있는 반면 용접식은 단 하나의 날이 있다. 재연삭이 필요하면 용접식은 공구고정구에서 용접생크를 제거한다. 삽입팁의 형태는 3각형, 4각형, 원형, 다이아몬드에서부터 여러 가지 특별한 모양까지 다양하다. 그림 2에서의 팁은 3각형으로 절삭에 사용할 수 있는 날이 6개이다. 초경합금 공구를 사용하면 더욱 많은 열이 발생하므로 적절한 냉각제의 공급이 필요하다.
공구재료
현재 생산전략은 공작기계에 관하여 엄격한 요구를 하고 있다. 공작기계에 부과되는 많은 요구조건을 수용하기 위하여 공구재료가 폭넓게 발전되어 왔다. 최선의 재료는 최저의 비용으로 가공품을 생산해 내는 것이다. 공구재료에 대하여 바라는 성질은 고온에서 연화되지 않는 성능, 낮은 마찰계수, 양호한 내 마멸성, 그리고 파단은 견디기 충분한 인성을 포함한다. 그림 3은 절삭속도에 대한 공구의 다양한 특성을 나타낸다. 그림3 A에서 공구 표면의 최대온도는 절삭속도에 관련된다. B에서 공구표면 온도가 증가함에 따라 표면경도의 대략적인 경사가 그려져 있는데, 로크웰 C로 측정되었다. 이 특성이 적열경도라고 알려진 것이다. 재질에 따라서 적열경도가 다르다.
초경합금
초경합금공구의 삽입팁은 분말야금 기술로써만 제작된다. 코발트와 탄화텅스텐의 분말을 형상으로 압축하고, 취급이 쉽도록 초벌 소결하고 최종형상으로 성형한 후, 1550°C에서 수소분위기 노에서 소결 한 다음, 연삭작업으로 다듬질한다. 탄화텅스텐은 합체하지 않으나 코발트를 첨가하고 소결을 거치면, 공구재질이 결합되어 분해되지 않는다. 코발트결합 탄화텅스텐계 재료는 최소 50년 동안 사용되고 있다. 긴 기간 동안 성공적인 이유는 열적 충격저항이 우수하고 고강도 및 고경도로 결합할 수 있기 때문이다.
'기계제작법' 카테고리의 다른 글
고속도강과 고탄소강에 대하여 공부하기 (0) | 2024.12.16 |
---|---|
초경합금에 대하여 공부하기 (0) | 2024.12.15 |
수직측면 프레스와 혼 프레스에 대하여 공부하기 (0) | 2024.12.14 |
프레스 가공과 작업에 대해서 공부하기 (0) | 2024.12.14 |
금속의 냉간가공에 대해서 공부하기 (0) | 2024.12.14 |